BPM (Business Process Management)
Implementamos a metodologia BPM (Business Process Management) é com uma abordagem que foca na análise, desenho, implementação, monitoramento e otimização contínua dos processos empresariais visando a redução de custos. Suas principais fases são:
-
Mapeamento dos processos
-
Redesenho (To be)
-
Indicadores (KPI’s)
-
Implementação das melhorias
-
Monitoramento
ADMINISTRATIVA
Lean Manufactoring
Aplicamos a ferramenta Lean na indústria a fim de maximizar a eficiência dos processos ao eliminar desperdícios, melhorar o fluxo de produção e, consequentemente, aumentar a performance operacional e a lucratividade da empresa. O foco do Lean está em agregar valor ao cliente com o mínimo de recursos possíveis, buscando continuamente otimizar a produção e eliminar atividades que não trazem valor ao produto final.
PRODUÇÃO
VSM (Value Stream Mapping)
A principal finalidade de aplicar VSM (Value Stream Mapping), ou Mapeamento de Fluxo de Valor, em uma indústria é identificar e eliminar desperdícios ao mapear visualmente o fluxo completo de processos que agregam valor a um produto, desde a matéria-prima até a entrega ao cliente final. Isso permite melhorar a eficiência dos processos, reduzir lead time (tempo total do processo), e otimizar o uso de recursos, com o objetivo de aumentar a performance operacional da empresa.
TPM (Total Productive Maintenance)
Aplicamos TPM (Total Productive Maintenance), ou Manutenção Produtiva Total, na indústria para maximizar a eficiência dos equipamentos e reduzir paradas não planejadas, aumentando a produtividade e a disponibilidade das máquinas. O TPM envolve todos os colaboradores, desde operadores até equipes de manutenção, na responsabilidade pela manutenção e pelo desempenho dos equipamentos, buscando eliminar falhas, defeitos e desperdícios.
Análise de Problemas
Implantamos ferramentas de análise como 8D, QRQC, Ishikawa, 5 porquês, de acordo com as necessidades detectadas na avaliação inicial in loco e o foco dessas ferramentas é a análise de causa raiz dos problemas e solução definitiva dos mesmos.
SMED (Single Minute Exchange of Die)
Realizamos todo a análise de setup estruturando o processo para que seja otimizado, além da redução expressiva de tempos o processo é reconcebido para reduzir as falhas.
5S, Gemba Walk, Auditoria Escalonada
Implantação de ferramentas para manter a padronização, atingimento de resultados e manutenção das atividades melhorando ainda o ambiente e a comunicação.

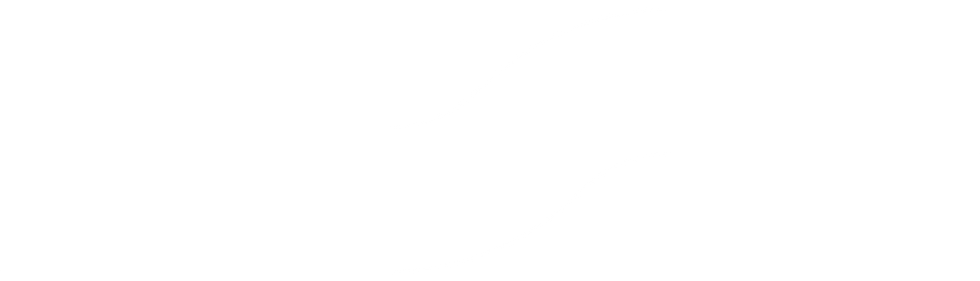